While Tony is living the high life at conferences and meetings throughout the Middle East, I’ve taken this opportunity to hijack TG’s technical blog; so for today only, welcome to “Steve’s Technical Blog”!
Last spring, the side of my head appeared in a blog entry about 3D Prototyping and Digital Modelling. One of the key points that was made was about backing up any digital models with good old fashioned hand calculations and proper testing. Well, that is exactly what this blog is all about.
For what now seems like an age, we have been operating a load monitoring service with pre-calibrated electronic swivel pins to measure the force acting within a hydraulic prop. An important part of this system is the test rig that we use to calibrate the load cells. The test rig itself is effectively a high strength hydraulic jack, within a frame, coupled to a very sensitive device for measuring force.
Using our test rig we can accurately measure an applied force which usually allows us to calibrate our pins very effectively. But this time, we have turned its talent for measuring forces toward crushing various arrangements of trench box prop couplings.
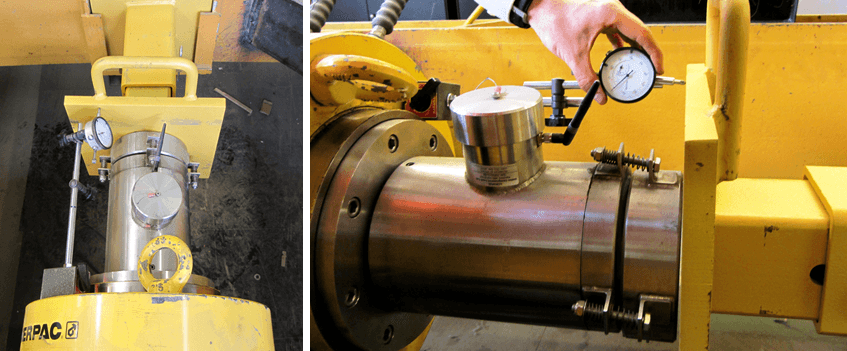
The images above show a trench box strut that is about to be put through its paces! Five minutes later and the test rig had done its duty and these were the results: elongated holes and a rather sorry looking pin.
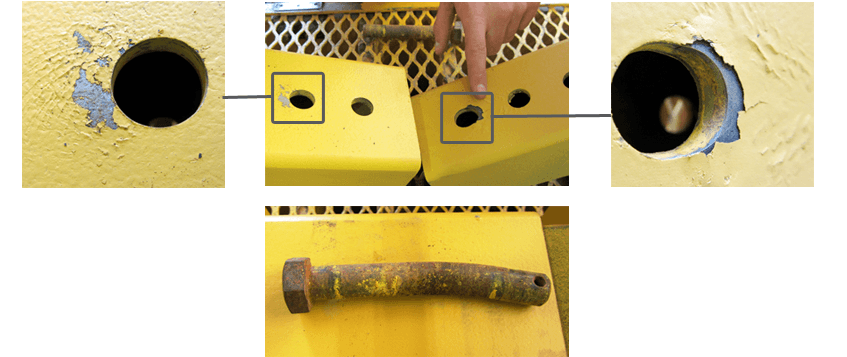
Yielding at 16 tonnes of force, the pin was almost exactly twice as strong as simple calculation would suggest… which considering the 2:1 factor of safety that we apply to these joints, really backs up the mathematics. So in summary, although it is more costly and time consuming to produce physical prototypes, not even the best numerical model can give an engineer the same confidence (and sense of satisfaction) as crushing a real life model in a 600 tonne hydraulic vice.