The project
With a fast-growing population forecast to reach two million by 2030, the Austrian capital, Vienna, is expanding its metro network on an ambitious scale. When completed, the network will have eleven new stations to accommodate the booming population.
Part of the project involves extension of the existing U2 line into the new U5 line terminating at a new station in Matzleinsdorfer Platz.
Civil engineering contractor Swietelsky has been carrying out preliminary work at Matzleinsdorfer Platz since 2018. The work now involves deep foundation work at Triester Strasse to protect surrounding buildings, install services and prepare for construction of the new underground station.
The challenge
A concrete piled diaphragm wall has already been installed at the site of the Trieste Strasse excavation and Swietelsky is now digging to a depth of more than 32m. Massive lateral loads are imposed by the surrounding soil and this requires robust bracing to prevent movement or collapse.
Normally, Swietelsky would have cast heavy reinforced concrete beams to brace the retaining walls at one storey above formation level until construction of the reinforced concrete floor slabs. However, it is precisely at this level that the new metro tunnels will enter the station – and that would require any concrete bracing to be demolished again. Swietelsky therefore needed a temporary bracing solution that could be easily installed and just as easily removed after installation of the floor slabs.
The solution
The most practical solution capable of providing the necessary support was the use of modular hydraulic bracing equipment.
Groundforce originally pioneered the development of this concept in the UK where it is now a well-established method for supporting deep excavations. More recently, Groundforce has successfully introduced the concept to other European markets, most notably in Scandinavia, Germany and Austria where more conventional techniques (e.g. bespoke steelwork fabrications) are still the norm.
Groundforce’s heavy duty support system comprises a range of hydraulically-extendible steel waling beams and tubular props that are installed around the perimeter of an excavation and across its width or across corners to counteract heavy ground pressure.
Since the system is modular, standard components can be employed to suit virtually any application and hydraulic rams give +/-500 to 1000mm adjustment as well as allowing pre-loading of the supports. The modularity of the system and its hydraulic adjustability results in a significant time and cost advantage compared to conventional shoring systems.
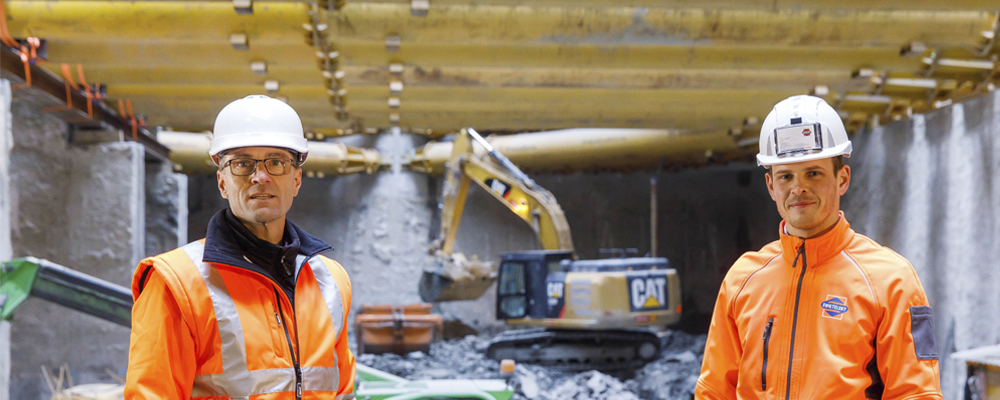
The equipment
The excavation is a slight rhombus shape in plan, measuring approximately 34m x 64m. Consequently, two of the corners are slightly less than 90o and the other two slightly more obtuse. Each of the four corners are braced with two levels of MP375 props varying in length from 6m to 24m. The MP375 is a medium-sized unit with a maximum support capacity of 375 tonnes and incorporates an external failsafe lock off system.
To brace the side walls of the excavation, Swietelsky has employed a single level of 12 MP750 (maximum capacity: 750 tonnes) transverse struts spanning from 31.5m to 34m across the excavation.
To prevent excessive flexing of the tubular steel props under their own weight at this extreme length, Swietelsky has supported them at their mid-point with steel beams sitting on temporary barrettes.
Delivery
Very close collaboration between the Swietelsky site team and the Groundforce technical and operations management team enabled meticulous planning of the delivery and installation process to meet exacting timelines. At all times, the focus was on speed of installation with zero compromise on health and safety.
Close to 1,000 tonnes of equipment was delivered to the site on a fleet of more than 40 vehicles over a three-to four-week period.
Every part of the process was carefully planned to reduce the risk of accidents. The components were lowered individually into the excavation through an opening in the concrete roof slab and made up to the required length within the confines of the existing concrete structures. In most cases the props were fully installed in less than an hour.
To further improve efficiency, the installation sequence was designed so that the end bearing plates and wall connections for each prop were pre-installed, ready to accept the prop itself, as the excavation progressed.
Groundforce despatched a site support team to assist the contractor and train Swietelsky’s team to install the props safely. The Groundforce team remained involved from start to finish and continued to provide support during the removal of the props, following a similar approach.
Installation of the Groundforce equipment started in early October 2020 and was completed within three and a half weeks. The equipment was supplied on a six-month hire contract, but the work was completed in just five months.
The modular components were dismantled and removed as the permanent works progressed. The basement slab was finished, and the last struts dismantled during the second week of March 2021.
The painstaking planning and preparation for this contract, and the ease of installation/extraction that resulted, saved valuable time for the project team. It has subsequently led to early technical collaboration between the parties on the next phases of the wider Vienna metro project where it is expecting to deliver the same positive benefits.
Swietelsky has secured 50% of the main contract work for the subsequent phases of the Vienna metro project; the other 50% has been awarded to a Porr/Strabag joint venture.
Swietelsky starts work on the first of its remaining phases in early 2022 and is currently in discussions with Groundforce to specify ground support requirements for the next phase. Porr/Strabag are also in early discussions with Groundforce to explore technical options. Work on the joint venture’s next contract begins in late 2022.
Client comments
Swietelsky confirmed that the Groundforce system demonstrated significant advantages in terms of construction time and structural stability.
Construction manager Lukas Schwalm also noted that the Groundforce system is more efficient and less wasteful than the alternatives: "All parts are reusable in contrary to conventional methods, which generate a considerable amount of debris during demolition," he said.