What is Pressure Testing?
What is the purpose of pressure testing?
Pressure testing is usually carried out after the installation of a pipeline and prior to its use; the purpose of this is primarily to:
- Give assurances to the integrity of the pipework
- Locate any leaks
- Check joints and fittings
Pressure testing is conducted to WIS 4-01-03 or IGN 4-01-03, depending on the pipe material, to ensure the pipe meets the required standards.
There are two primary methods for pressure testing: hydrostatic testing and pneumatic testing. Whilst the former uses water as the test medium, the latter uses air.
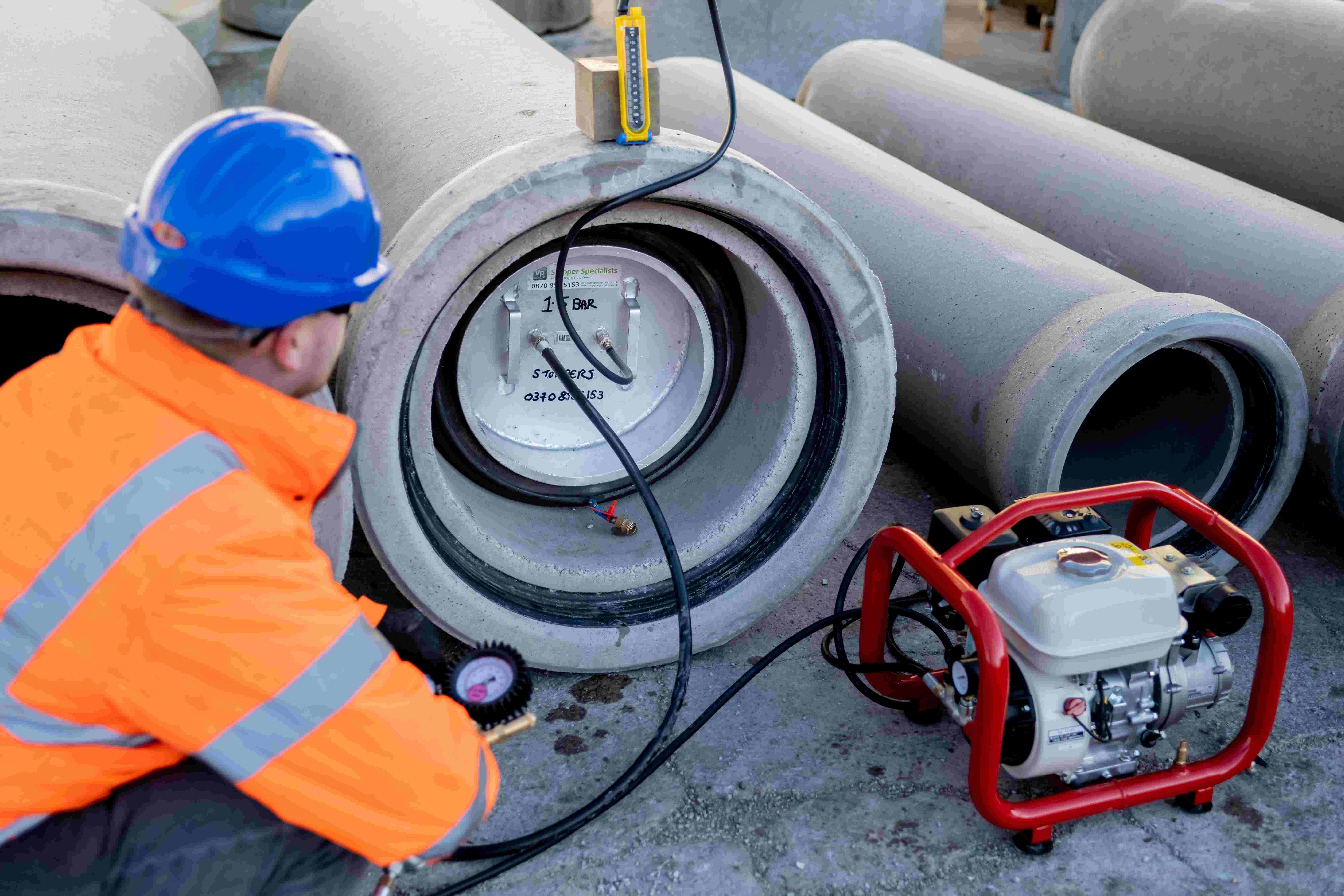
When is pipe pressure testing undertaken?
Pipe pressure tests are usually completed following the installation of an underground pipeline or after conducting work such as electro-fusion welding or jointing. This is done to maintain safety standards and to ensure that heat has not caused the mechanical properties of the pipe or its fittings to become compromised. Pipe pressure testing is also done in the following instances:
- During commissioning of new pipelines for the water, wastewater, construction and petrochemical industries.
- As part of planned or routine maintenance
- For regulatory compliance to meet industry standards (WIS 4-01-03 / IGN 4-01-03).
WIS 4-01-03
IGN 4-01-03
Hydrostatic pressure testing
A hydrostatic pressure test is achieved by filling a pipe with water so the pipe can be checked for any leaks or changes in shape. The pipe section is isolated using valves, flanges or other means, then water is pumped into the system until the section is filled but only the static head pressure is present (no additional pressure). Depending on the pipe material, the pressure is then increased to the desired Maximum Design Pressure (MDP) and maintained for an hour or more. The specific procedure for testing in the water industry is written in the aforementioned standards. See below link for our Pressure Testing Equipment range:
What is pneumatic pipe testing?
Pneumatic/air testing is used to perform low level testing on drainage installations where the system isn’t expected to be under significant pressure during its lifetime, for example is gravity fed or otherwise. Air testing involves using specifically designed pipe stoppers that can be secured in the pipe and then air can be introduced into the pipe using a small hand bellow and air test kit. See link below for our Air Test Stopper range:
Air Test Stoppers
Why is Pneumatic Testing more risky than Hydrostatic testing?
The results produced by pneumatic testing are indicative of adequate or defective pipework and can be implemented quickly. Whilst low level air testing is widely used in sewer and drainage applications, for potable/clean water testing, hydrostatic testing is recommended as the risks of catastrophic failure are much lower. Air is 20,000 times more compressible than water, and therefore stores huge amounts of energy when under pressure. If a pipe joint or fitting were to fail, then the energy release presents a significant risk to those in the working area.
Air content is also a consideration when performing hydrostatic pressure testing as air can enter the system through pumping or through open valves/fittings. Generally the pipe system requires less than 4% air in the system for a hydrostatic test to remain valid. This is because excessive air content can increase the pressurisation time and/or heightens the risk in the event of a failure.
Want more information on Pressure testing equipment?
Stopper Specialists, home of the Pressure Test+ app, are the leading provider of pipe stoppers, pressure testing, and associated equipment, consistently striving for excellence and innovation in all aspects of our operations. From blanking off vessels to conducting advanced pipe pressure testing, we cater to the needs of utilities, civil engineering, construction, petrochemical, agricultural, and manufacturing sectors.
To find out more about the full range of products and services offered by Groundforce, call on 0370 850 5153 or email on groundforce@vpplc.com.